Unlocking the Power of Welding WPS: Techniques for Performance and Safety in Construction
In the realm of construction, Welding Treatment Requirements (WPS) stand as the backbone of welding operations, determining the needed actions for attaining both efficiency and safety and security in the manufacture process. Understanding the ins and outs of WPS is paramount to using its full potential, yet several companies struggle to unlock real power that lies within these records (welding WPS). By diving into the methods that enhance welding WPS, a world of boosted performance and increased safety and security waits for those ready to check out the nuances of this vital facet of construction

Importance of Welding WPS
The importance of Welding Procedure Specs (WPS) in the construction market can not be overstated. WPS act as a vital roadmap that outlines the needed actions to ensure welds are performed constantly and correctly. By specifying important specifications such as welding processes, materials, joint layouts, preheat temperature levels, interpass temperatures, filler steels, and post-weld warm treatment needs, WPS give a standard strategy to welding that improves effectiveness, high quality, and safety and security in fabrication procedures.
Adherence to WPS aids in achieving harmony in weld high quality, reducing the chance of flaws or structural failures. This standardization also facilitates compliance with industry guidelines and codes, ensuring that made structures satisfy the called for safety criteria. In addition, WPS documents makes it possible for welders to reproduce successful welding treatments, resulting in regular results across various projects.
Fundamentally, the thorough development and strict adherence to Welding Procedure Requirements are vital for promoting the integrity of welded frameworks, protecting against prospective hazards, and upholding the online reputation of fabrication business for delivering premium product or services.
Crucial Element of Welding WPS
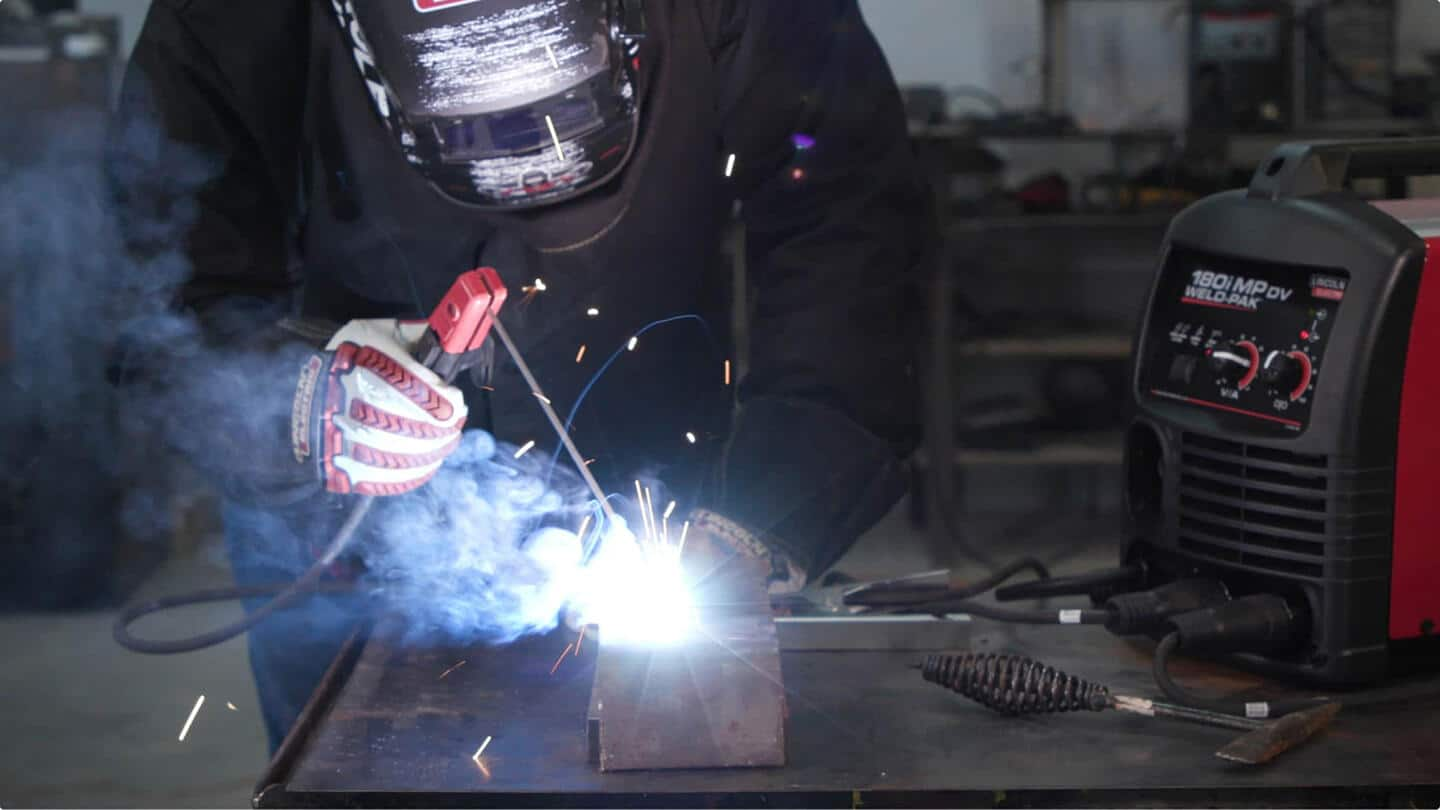
Enhancing Efficiency With WPS
When maximizing welding procedures, leveraging the key elements outlined in Welding Procedure Requirements (WPS) becomes important for optimizing and enhancing processes efficiency. One means to improve efficiency with WPS is by very carefully selecting the appropriate welding specifications.
Frequently evaluating and updating the WPS to include any type of lessons learned or technological improvements can also add to efficiency renovations in welding operations. By embracing the guidelines set forth in the WPS and continuously seeking means to maximize procedures, makers can accomplish higher performance levels and superior end results.
Ensuring Safety in Construction
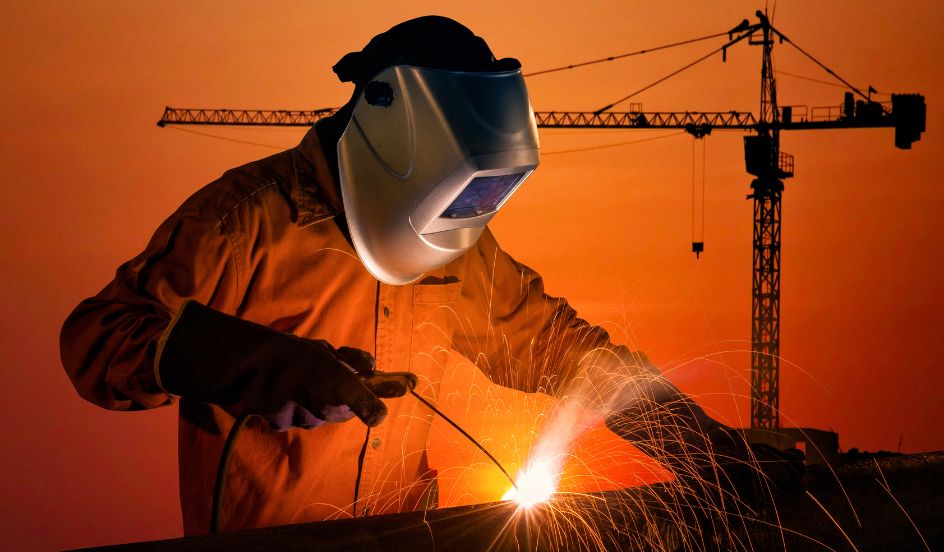
Making certain safety in manufacture involves a multifaceted method that encompasses numerous facets of the welding procedure. Welders must be equipped with proper gear such as helmets, gloves, and protective apparel to minimize dangers associated with welding activities.
Moreover, adherence to proper air flow and fume removal systems is vital in preserving a healthy work atmosphere. Welding fumes have harmful materials that, if breathed in, can posture severe health dangers. Executing efficient ventilation procedures aids to minimize direct exposure to these unsafe fumes, advertising respiratory system health and wellness amongst employees.
Normal tools upkeep and examinations are also necessary for ensuring security in fabrication. Defective equipment can lead to accidents and injuries, highlighting the value of routine checks and prompt repair work. By focusing on precaution and cultivating a society of understanding, manufacture centers can create a safe and secure and productive workplace for their employees.
Applying WPS Ideal Practices
To improve functional efficiency and make sure high quality results in fabrication processes, including Welding Treatment Requirements (WPS) finest methods is vital - welding WPS. Applying WPS finest practices entails careful preparation, adherence to sector requirements, and continual tracking to assure ideal results. First of all, selecting the proper more welding procedure, filler product, and preheat temperature level defined in the WPS is essential for achieving the wanted weld quality. Second of all, making certain that qualified welders with the required certifications lug out the welding treatments according to the WPS standards is necessary for uniformity and reliability. Routinely updating and reviewing WPS papers to show any type of process improvements or adjustments in products is additionally a key ideal method to keep accuracy and relevance. Furthermore, giving extensive training to welding personnel on WPS demands and ideal practices promotes a society of security and top quality within the fabrication atmosphere. By diligently executing WPS ideal practices, makers can streamline their procedures, decrease mistakes, and deliver exceptional products to meet client assumptions.
Final Thought
In conclusion, welding WPS plays a critical duty in ensuring performance and security in manufacture processes. By concentrating on essential components, improving efficiency, and carrying out ideal practices, business can enhance their welding operations. It is important to focus on precaution to stop accidents and guarantee a smooth manufacturing procedure. By following these strategies, businesses can open the full potential of welding WPS in their construction procedures.
In the world of construction, Welding Treatment Requirements (WPS) stand as the foundation of welding procedures, dictating the required steps for accomplishing both performance and safety and security in the construction procedure. By specifying essential criteria such as welding processes, materials, joint layouts, preheat temperatures, interpass find out here now temperatures, filler he said steels, and post-weld warmth therapy demands, WPS offer a standard technique to welding that improves effectiveness, quality, and safety and security in construction processes.
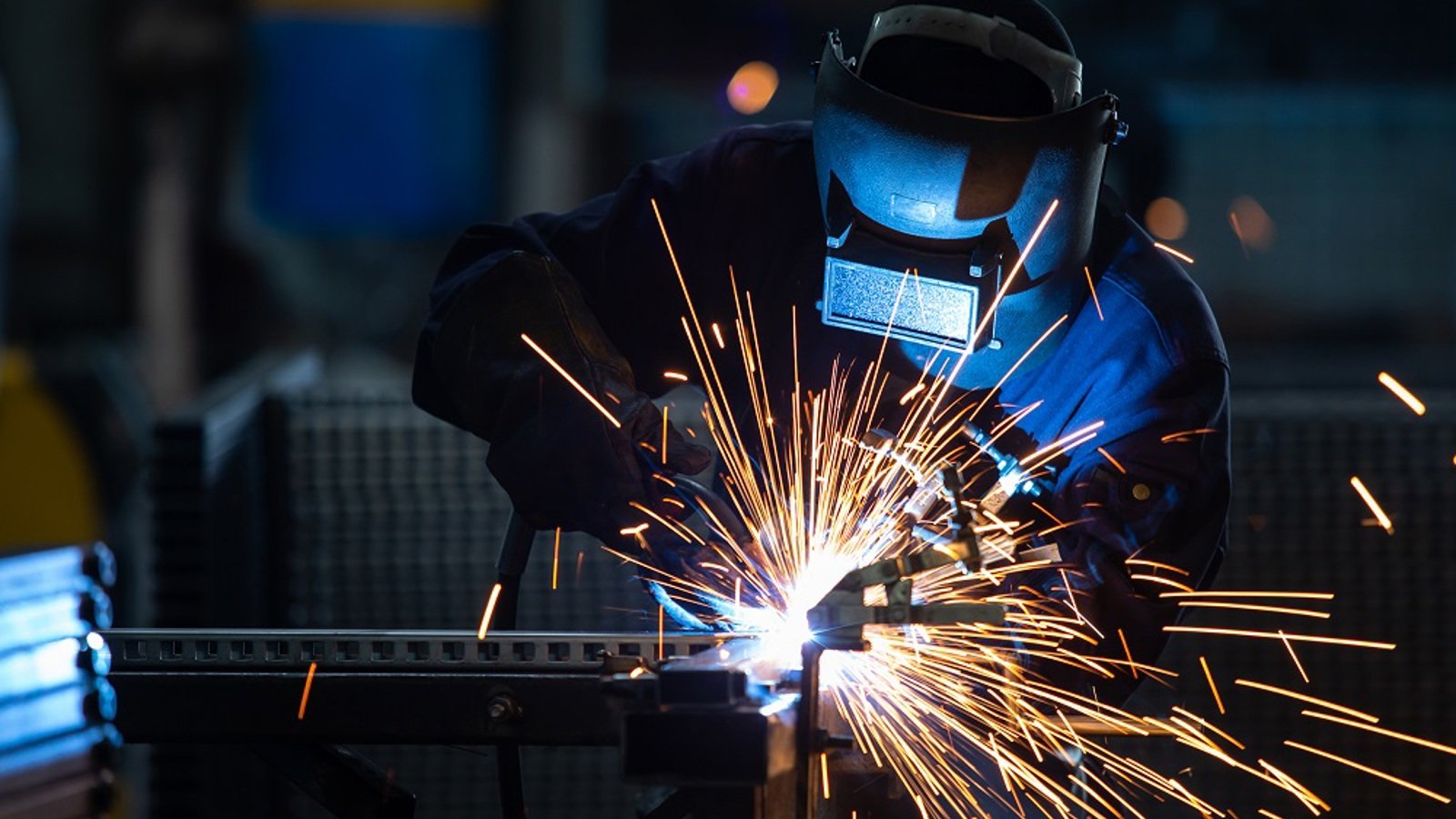
When enhancing welding operations, leveraging the key elements laid out in Welding Treatment Specs (WPS) becomes essential for simplifying processes and optimizing productivity. (welding WPS)